
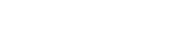



Country Websites
Business Websites
MISTRAS’ in-depth lab testing services detect material flaws and discontinuities introduced in the manufacturing process that can degrade the structural and operational integrity of your components and assets.
Even the smallest flaws in your assets and equipment can contribute to the development of larger defects, risking operational interference and even complete asset failure.
Whether they are caused by environmental influence, faulty production, or use-related stress, flaws in any componentry should be quickly identified and addressed.
Welding flaws compromise the usefulness and function of the weld, which can lead to more serious defects and damage within your facility. The causes of welding flaws include poor process conditions, operator error, flawed technique, bad weld grooves, and incorrect consumables. In addition, hydrogen embrittlement and residual stresses can cause flaws in welding while it is in use.
Welding flaws create a huge hazard for the structural and operational integrity of your assets. Some prominent welding flaws that MISTRAS detects include:
Some other common types of welding flaws that can affect welds include lamellar tearing, overcut, and gas inclusion.
In the aerospace and oil & gas industries, material flaws can have serious consequences on the safety and fitness for use of components and assets by greatly decreasing material strength.
Even small material flaws can accumulate into larger defects or accelerate further damage when assets undergo the intense stress that accompanies regular operation. Plastics, metals, composites, and a wide variety of other materials can experience an array of flaws, which is extremely detrimental in any context.
Key flaws in this segment include:
Some other common raw materials and machined parts flaws include:
Casting flaws include any irregularities or discontinuities that occur during the metal casting process. When the casting process is interrupted, flaws can occur in a material, including surface and subsurface defects.
These flaws occur as a result of a variety of casting process discontinuities, including flawed:
Casting flaws can cause problems for any assets that require componentry of a specific shape and composition, along with decreasing the strength and integrity of the metal.
When these casting process irregularities occur, it can quickly lead to material defects, some of the most common including:
MISTRAS has the capabilities to identify a huge range of flaws in newly-fabricated components and materials to ensure operational integrity. We offer advanced lab services to closely inspect materials through: