
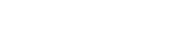



Country Websites
Business Websites
Cracking is a common damage caused by stress in a material that can easily be exaggerated by other factors, including corrosion, fatigue, high pressure, and material of construction.
Cracking affects a variety of materials across multiple industries, including metals, concrete, paint, asphalt, and other protective coatings and building materials.
Since cracks create a physical separation within solids, they greatly reduce strength and degrade structural soundness, creating a huge risk for your facility’s assets and personnel.
MISTRAS expertly detects a wide range of cracking damage mechanisms, some of which are detailed below.
Hydrogen Induced Cracking (HIC) may occur in pressure equipment that contains Wet Hydrogen Sulfide (H2S) environments.
The defects are caused when hydrogen blisters form, in turn causing cracks that link these blisters together into larger defects. Since the blisters form at various depths, the cracking will appear as a stair-step appearance, sometimes called “stepwise cracking.”
The high-concentration hydrogen environments that breed this type of damage are common in refinery process environments, specifically targeting steels with a hardness of 22 or greater on the Rockwell C scale.
High Temperature Hydrogen Attack (HTHA) occurs in steel and steel alloys when the material is exposed to elevated temperatures.
At these high temperatures, hydrogen molecules break into hydrogen atoms, which diffuse into steel to create methane gas. Upon accumulation of methane within steel, bubbles are formed which connect to create micro-fissures at grain boundaries and expand into material cracking.
HTHA is a common defect in refining, manufacturing, and petrochemical plants. HTHA results in a variety of defects for steel assets, including decarburization, reduced strength, or even complete asset failure.
Click here to learn about our special emphasis programs for detecting and preventing HTHA cracking.
Surface cracking attacks concrete to reduce strength and break down concrete structures. It can be caused in virtually any environment, resulting from a number of different factors, such as thermal contraction, subgrade settlement, applied loads and stress, and shrinkage.
In any concrete application, surface cracking can be extremely dangerous. In infrastructure assets like highways, bridges, and structural foundations, concrete cracking can weaken assets to the point of complete failure, creating enormous public safety hazards.
Stress Corrosion Cracking (SCC) is a material defect commonly found in ductile metals, caused by the combination of corrosion and tensile stress.
Tensile stress on an asset can be caused by stress from various operational activities, including welding, heat treatment, forming, and grinding, and can be exaggerated by the build-up of corrosion in confined spaces.
SCC cracking can be microscopic, making it extremely hard to detect, but it can degrade long-term integrity in metal assets.
Some other forms of SCC our customers commonly deal with include:
Wet Hydrogen Sulfide (H2S) cracking is a defect common in oil & gas and petrochemical assets in which aqueous hydrogen creates hydrogen sulfide corrosion cracking to degrade steel materials.
When steel assets have irregularities or impurities, hydrogen can collect in these open spaces and cause damage when the asset is located in a wet H2S environment.
This type of damage is extremely difficult to detect with only visual inspections (VT) techniques, and can cause devastating damage to assets, especially in hard-to-reach locations like vessel interiors.
With inspection, engineering consulting, monitoring, and maintenance solutions available for multiple forms of cracking damages, MISTRAS helps you detect and mitigate cracking as early as possible.
We offer comprehensive, proceduralized programs to identify and mitigate HTHA cracking. We also offer an online monitoring solution for the early detection of stator vane cracking in gas turbines. Our maintenance teams are also equipped to repair minor cracking.