
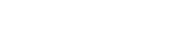



Country Websites
Business Websites
MISTRAS Group’s Guided Wave Testing (GWT) services utilize advanced NDT technology to remotely analyze assets for corrosion and flaws over long distances without the need for direct contact.
Piping systems can present problems for inspections, due to their often unorthodox shapes and locations. Traditional ultrasonic (UT) inspection sometimes requires direct contact and access to these hard-to-reach areas, which can at times be impossible. To make for a more reliable and efficient inspection process, MISTRAS can use GWT to transmit volumetric ultrasound waves into structures from a distance.
Facilities are moving towards condition-based inspection programs to enhance mechanical integrity and preventative maintenance. GWT inspection services are a long-range Advanced Non-Destructive Testing (ANDT) solution for asset corrosion detection, helping to prevent critical production losses and crucial asset damage.
Guided Wave UT is used to rapidly inspect pipelines, piping systems, and other assets with minimal insulation removal. GUL quickly localizes cracking and corrosion damage to pinpoint and characterize length and depth. It is often used for unpiggable pipelines and for pipes resting on supports, making them susceptible to point-of-contact corrosion, or touchpoint corrosion (TPC).
GWT inspections are customizable to specific asset needs. Transducers are designed and placed so that the appropriate wave modes are transmitted into the structure. It is critical to ensure the correct ultrasonic wave mode is being used for the specific scan application.
The technology utilizes torsional and longitudinal waves to inspect large sections of piping from one location. Inspections begin with a collar around a pipe section. Individual scans, referred to as “shots”, are conducted, reflecting girth welds, corrosion, and cracks from fixed reference points.
MISTRAS uses software to analyze these reflections to produce information on the probability, approximate size, and location of the flaws. Reports can be comprehensive or concise, depending on client preferability. Supporting documents such as Quantitative Short Range (QSR) B-Scan images, photographs, Time of Flight Diffraction (TOFD) screen-captures, and Large Structure Inspection (LSI) scans can be imported into the report.
Long-range ultrasonics make for an effective method in screening damage without needing to access a hard-to-reach section of piping. GWT offers key benefits that set it apart from traditional inspection methods, including:
GWT can be used for a wide range of applications, including:
Corrosion under insulation (CUI), touch point corrosion, and soil to air transitions are key damage mechanisms identified by GWT. The waves can locate internal and external defects along pipelines.
MISTRAS’ Permanently Installed Monitoring System (PIMS), which uses GWT technology, can be installed in various locations, including buried piping applications, to periodically monitor suspect areas without having to dig trenches for subsequent inspections. In advanced implementations of this solution, MISTRAS enables operators to extract wall thickness measurements around the pipe to establish short and long-term corrosion rate calculations.
The technology is also used as part of PMI Retrofit programs to locate piping welds between attachments.
MISTRAS Group performed GWT services for a major US refinery with several different piping systems including elevated, buried, insulated and piping resting on supports. Over 2,000 shots were performed throughout the project while scanning for damage mechanisms. To ensure GWT results were accurate, the refinery implemented follow-up procedures including manual ultrasonics, semi-automated ultrasonics, and material sectioning of suspect areas.
After all inspections were completed, it was determined that the inspection performed by MISTRAS yielded a reliability correlation factor of 99%.