
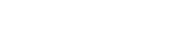



Country Websites
Business Websites
MISTRAS Group’s Phased Array Ultrasonic Testing (PAUT) is ideal for rapid and detailed inspection for slewing bearing components on deck cranes, which can be susceptible to major cracking.
Slewing bearings on on-board deck cranes are essential elements of conventional cranes, but as critical parts of major weightlifting, flaws can emerge. These bearings in motor vessel (M/V) ship deck cranes can suffer from fatigue stress, leading to cracking in critical, high stress areas. The top and bottom inner corners of the protruding slewing ring can be specifically susceptible to cracking. MISTRAS’ capabilities allow sensitive areas of the bearings to be reached and defects to be located efficiently.
MISTRAS Group’s Phased Array Ultrasonic Testing (PAUT)-based technique for early detection of critical fatigue cracks uses specific phased array probes for detection and sizing of cracks in the affected areas. The complex geometry and difficult-to-detect direction of the cracks on cargo ship rotating cranes require a specialized inspection procedure. Prior to testing, MISTRAS will review the drawing to assess testability of any specific bearing.
While the crane is out of service, inspection is performed from the upper side of the slewing bearing by using a position encoder. The encoder saves the entire inspection and the results can be analyzed and evaluated after the process. The inspection is fast, allowing for up to three cranes having slewing bearing of 2300 mm diameter to be reviewed on one date with limited preparation.
Being proactive about asset integrity can be the deciding factor in whether operations are unexpectedly halted. Early detection of fatigue cracks promotes responsible crane usage and prevents damages from hurting production down the line. Application advantages of PAUT for slewing bearings include:
Thanks to MISTRAS’ optimized processes, little site preparation is needed prior to inspection. Preparation requirements to conduct the test are:
After field analysis is completed, the formal inspection report contains the key results and findings operators need. Processed with reliable software, reports are saved and stored for convenient access and retrieval.
Screenshots of discovered cracks are included to visualize the state of the asset condition. An estimation of the deepest crack found is given. Horizontal and vertical dimensions of cracks are shown to accurately relay the severity of damage. Based on MISTRAS Group’s accessible inspection results, a course of action and necessary maintenance can be determined to solve the defects.