
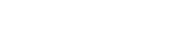



Country Websites
Business Websites
';document.currentScript.insertAdjacentHTML('afterend',preloadTag);
Eddy Current testing inspection (EC) is a highly-versatile branch of non-destructive testing (NDT) that is sensitive to small cracks and is able to detect surface and near-surface defects.
Since eddy current (EC) equipment is often portable, immediate results are available and minimum part preparation is required. Probes also do not need to directly contact the material, so its inspection capabilities extend to conductive materials with complex shapes and sizes.
A critical component of any eddy current examination is the ability to calibrate the unit based on reference standards manufactured from the same or very similar material as the test specimen. In the case of tubing inspection, an ASME tubing pit standard is required, and MISTRAS teams are trained to comply with these regulations.
The eddy current technique encompasses several branches of inspections, including:
Read more about out advanced PEC & PECA inspection services here.
Eddy current testing is most commonly used for tubing inspection in the power generation and oil and gas industries. It is also effective for crack detection (especially in the aerospace industry) and conductivity measurements for material identification and material sorting.
Other applications include:
The inspection of shell-and-tube heat exchangers is commonly performed with eddy current testing (EC), which can be used on non-magnetic (non-ferrous) and slightly magnetic alloys that are conductive. This equipment allows the technicians to accurately inspect twisted tubing in real-time, by enabling full-length recording and offline data analysis.
MISTRAS Group provides highly-qualified, trained eddy current inspection technicians for the inspection of Twisted Tube® heat exchangers. Twisted Tube® heat exchangers have become increasingly popular in the refining, petrochemical, and chemical industries, and eddy current testing has been successful in the inspection of these important assets because of its ability to detect small defects, such as stress corrosion cracking.
MISTRAS’ EC inspection equipment allows technicians to accurately and confidently inspect twisted tubing in real-time, by enabling full-length recording capabilities. This allows offline data analysis to assess damages with the customer. MISTRAS heat exchanger inspection services also include on-site and in-house data analysis.