
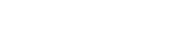



Country Websites
Business Websites
';document.currentScript.insertAdjacentHTML('afterend',preloadTag);
MISTRAS has extensive experience conducting Fitness-for-Service (FFS) assessments to evaluate mechanical integrity in pressure vessels, piping, storage tanks, and more.
Industrial assets that have been in operation may develop degradation and damage of construction materials due to either normal or abnormal operating conditions. Critical damage mechanisms can occur in a short or a long operation term, involving equipment failures affecting a safe and reliable operation. An unplanned asset shutdown due to equipment failure is expensive in terms of both missing production, resulting in loss of revenue, and resources required to fix a particular mechanical integrity issue.
To help operators maximize uptime and equipment lifespans, MISTRAS provides decades of expertise and an industry-leading breadth and depth of inspection services and technologies to perform code-compliant inspections and Fitness-for-Service (FFS) assessments.
Field inspections are a critical part of FFS assessments, as they provide the necessary data to evaluate the condition of pressure vessels, piping systems, and tanks. As an industry leader in non-destructive testing (NDT), MISTRAS employs a wide range of advanced and traditional NDT services, including advanced, proprietary digital inspection technologies, to detect internal and external flaws without compromising the equipment's integrity.
Standards like API 510, API 570, and API 653 guide these inspections:
These inspections are essential for gathering real-world data about the condition of equipment, enabling MISTRAS to provide mitigative recommendations for indications found.
Data from these integrity approaches can be centralized in MISTRAS’ world-class Asset Integrity Management Services (AIMS) software, Plant Condition Management Software (PCMS®) by MISTRAS.
FFS assessments play a key role in assessing the severity of identifying potential issues like corrosion, cracks, or wear. An FFS assessment is an industry-recognized practice developed to assist operators in managing mechanical integrity of their assets, as well as making run-repair-replace documented decisions by determining if equipment is safe for immediate return to service. It comprises a rational basis for defining material damage acceptance. FFS of equipment may be viewed both in terms of current and future condition or remaining life.
API 579 and ASME FFS-1 provide comprehensive guidelines for conducting FFS assessments. The standard is divided into three levels of evaluation:
With a low-level assessment, a decision can be taken in a short period. A higher level of assessment is complex and time-consuming but still require less time and cost than ordering, supplying, and commissioning of replacement equipment. These levels help operators determine the fitness of equipment and make informed decisions on repair or continued operation.
Following FFS assessments, the ASME VIII Code Calculation is often used for re-rating pressure equipment. This process recalculates the Maximum Allowable Working Pressure (MAWP) of an asset, taking into account its current condition and any degradation found during inspections. Additionally, Process Safety Information (PSI) is generated for pressure equipment to document critical details such as design specifications, material properties, and operating conditions. This information is vital for ensuring safe operation and regulatory compliance.
There are numerous benefits to adding FFS assessments to an asset integrity management program. Conducting FFS assessments supports reliability of process facilities and reduces challenges related to expenditure and assessment completion time. Planning for an integrity assessment can save time collecting the data required to complete the assessment. Including FFS approaches as part of maintenance programs can save costs during facilities outages. Ensuring that these capabilities exist can reduce duration of shutdowns and potentially avoid unplanned shutdowns. MISTRAS has a proven track record in conducting comprehensive FFS assessments that have benefited industry operators by supporting:
Whether it is a single FFS assessment, Suitability-for-Service assessment of an undocumented pressure vessel or a large process facility condition assessment for a service life extension program, MISTRAS' qualified and certified FFS engineers have the expertise needed to help keep your assets operating safely, effectively, and in compliance.