
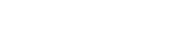



Country Websites
Business Websites
';document.currentScript.insertAdjacentHTML('afterend',preloadTag);
Since 1978, MISTRAS Group has served as a global leader in developing and manufacturing Acoustic Emission (AE) equipment for industrial inspection and monitoring applications.
Acoustic Emission (AE) technology ‘listens’ to your equipment, using specialized sensors to detect discontinuities in your equipment. Discontinuities and defects in a material produce stress waves, which then propagate to the material’s surface and are picked up by the active AE sensing technology. By converting these waves into electrical signals, AE is an ideal technique to effectively assess the behavior of materials under stress.
Originally founded in 1978 as an AE equipment manufacturer, MISTRAS is a global leader in developing and manufacturing state-of-the-art AE inspection and monitoring equipment for spot inspections and long-term, unattended monitoring. Our expert engineers and scientists bring decades of experience in working with our customers to design AE systems that solve their most difficult asset protection problems.
MISTRAS offers an expansive range of AE products & systems, in addition to all related sensors, data acquisition software, and accessories, including:
Our hardware-as-a-service model means we don’t just sell you equipment; we offer 24/7 training and monitoring support so you can stay aware of your asset’s conditions and informed of any high-consequence damages at all times.
As an industry-leading developer and manufacturer of acoustic emission inspection and monitoring equipment, customers rely on Physical Acoustics solutions for some of their most critical asset integrity needs. Some of the most popular solutions include:
An extremely versatile method of inspection, AE can be used across many industries to identify flaws and perform condition assessments in equipment and componentry of a variety of materials. Some common defects identified include:
If these defects go undetected, they can accumulate and grow into much more substantial damage, risking serious consequences for asset safety and integrity. MISTRAS' AE solutions can identify small-scale damage as soon as it occurs, creating the opportunity for repair and maintenance to be completed before the risk of asset failure becomes imminent.
Our inspection and monitoring equipment enables our customers to make more informed maintenance decisions on their assets, by alerting them to which assets need to be taken offline and repaired immediately, and which can be delayed until a scheduled work outage.
Offering AE inspection & monitoring solutions to customers in the aerospace & defense, infrastructure, manufacturing, oil & gas, power, and academia & research industries, our customers commonly use our AE solutions assess and track the condition of:
As a non-destructive testing (NDT) technique, AE can be used to inspect or monitor assets while they remain in-service. This enables our clients to use our solutions to track changes in their asset’s condition without having to shut down operations, reducing downtime and enhancing productivity.
Some other advantages of MISTRAS' acoustic emission solutions include:
What's Next?
Fill out the form to be contacted by our Acoustic Emission (AE) Equipment experts.
Submit form to be contacted